
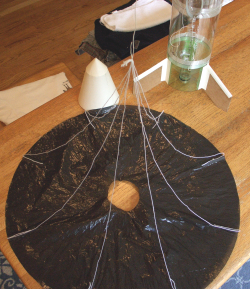
It was a fair challenge - until I found this video. In short, it was not and I have a decent portion of a journal/log filled with my experience on the development throughout the season with diagrams and descriptions of how the flights went (wrote in that same log for the next season, which featured an altimetry based challenge - I have a special design that I might post at a later date). I decided to participate in the Science Olympiad Egg-O-Naut Challenge, and so I thought that developing a system to recover an egg would be easy. I like the idea of using something that is elegant in it's simplicityĪnother pretty dank late reply: Not my video, but I have based a design off of this dude's parachute deployment mechanism. I have seen more involved deployment mechs using large flaps, etc to open the chute bay.

I'm intrigued by the idea of using only air resistance to remove the cone. We ended up with many early deployments and one shredded chute Our next test will be to snug the cone up a bit and test with different flap sizes to find he optimum balance between minimal drag during launch and ease of deployment. The main issue was during higher pressure launches, the cone would sometimes be ripped off/lifted off during launch shortly after burnout. We had a great record with this deploy method even while reducing the flap size to minimal.
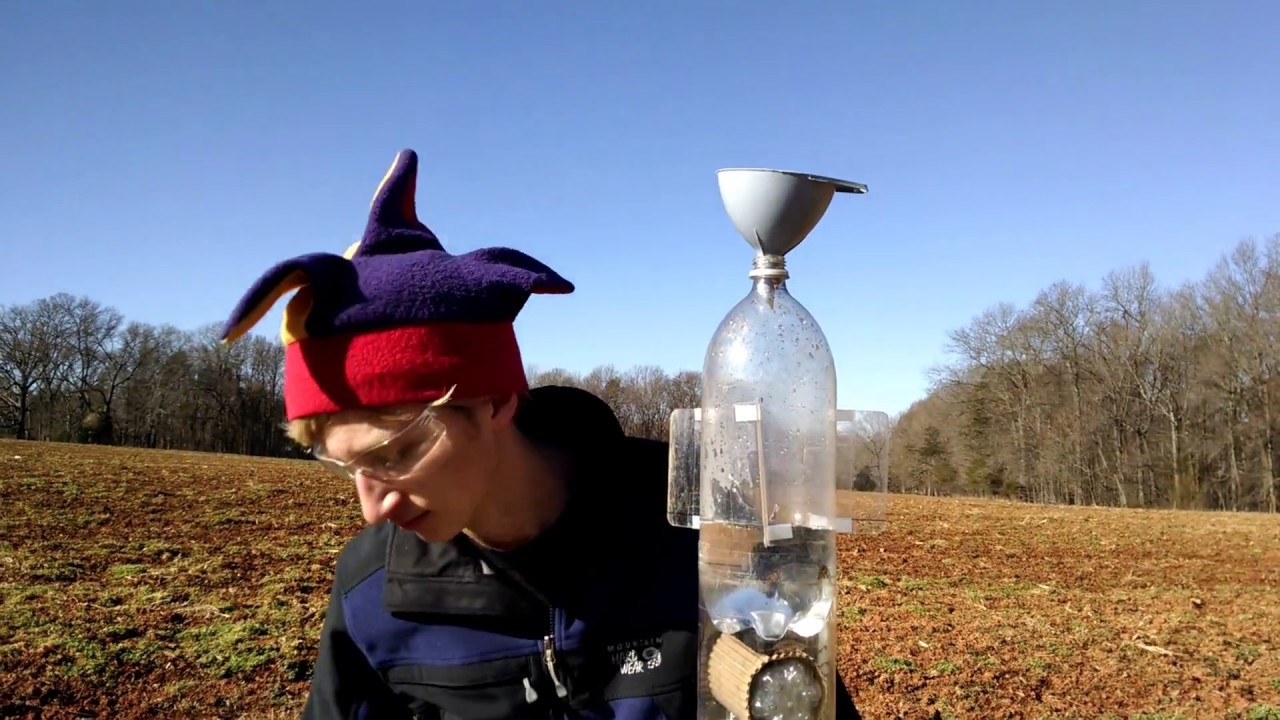
The cone again had a loose fit such that even the weight of the chute would pop the cone off if inverted while stationary. The flap would act to lever the cone off the body deploying the chute. The thought being the flap would offer minimal resistance during launch, but offer greater resistance through apogee and descent. I expect that increasing the drag on the rocket body may help this, however this leads to another problem.Ī second system tried involved adjusting the weight balance of the rocket to behave like a backglider, but with an air flap mounted to the lip of the nose cone. It appears that the air pressure held the cone to the rocket. The cone had a very loose fit such that inverting the rocket would cause the cone to fall off. It turned out to be unreliable and we ended up with quite a few lawn-dart landings. I've tried weighting the nose cone to encourage it to slip off during deceleration/apogee. Would love any feedback or advice from others. Non-electronic) parachute deploy system that could be easily integrated into a 2l rocket.
